푸츠마이스터 스플라인 샤프트
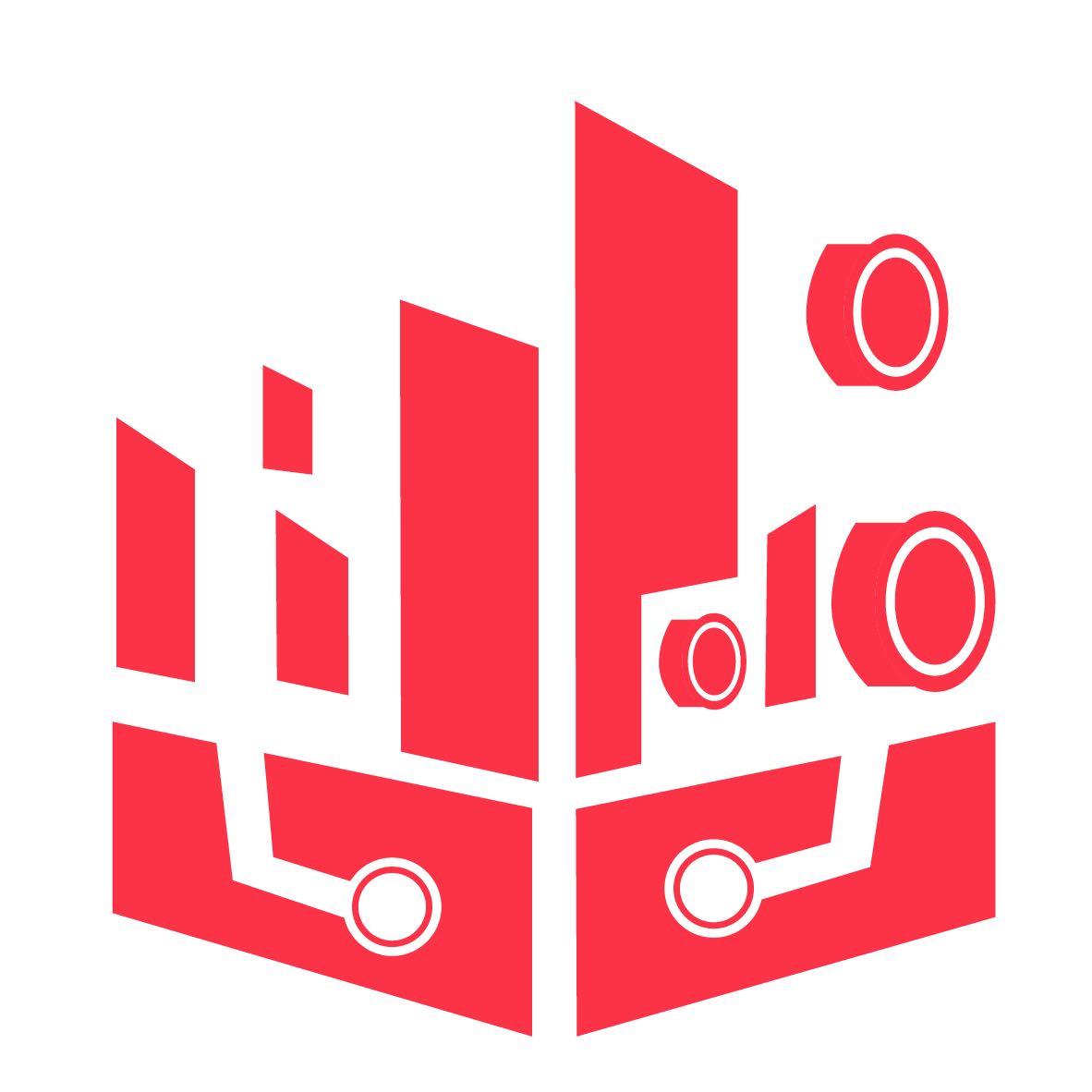
설명
드라이버 샤프트는 건설 기계 섀시의 구동 부분의 핵심 부품 중 하나입니다.사용 중에 복잡한 굽힘, 비틀림 하중 및 큰 충격 하중을 받기 때문에 세미 샤프트에는 높은 피로 강도, 경도 및 우수한 내마모성이 필요합니다.세미 샤프트의 수명은 제품 공정 설계 단계의 계획 및 재료 선택에 의해 영향을 받을 뿐만 아니라 단조품 생산 공정 및 단조품의 품질 관리도 매우 중요합니다.
생산 공정의 공정 품질 분석 및 제어 조치
1 절단 공정
블랭킹의 품질은 후속 자유 단조 블랭크 및 심지어 다이 단조의 품질에 영향을 미칩니다.블랭킹 공정의 주요 불량은 다음과 같습니다.
1) 길이가 허용범위를 벗어났습니다.블랭킹 길이가 너무 길거나 너무 짧으면, 너무 길면 단조품의 크기와 재료 낭비가 지나치게 커지는 원인이 될 수 있고, 너무 짧으면 단조품이 불만족스럽거나 크기가 작아지는 원인이 될 수 있습니다.그 이유는 포지셔닝 배플이 잘못 설정되었거나 블랭킹 프로세스 중에 포지셔닝 배플이 느슨하거나 부정확하기 때문일 수 있습니다.
2) 단면의 경사가 크다.끝 표면 경사가 크다는 것은 세로 축에 대한 블랭크 끝 표면의 기울기가 지정된 허용 값을 초과한다는 것을 의미합니다.단면의 경사가 너무 크면 단조시 주름이 생길 수 있습니다.그 이유는 블랭킹 중에 바가 고정되지 않았거나 띠톱날의 톱니 끝이 비정상적으로 마모되었거나 띠톱날 장력이 너무 작거나 띠톱 기계의 가이드 암이 동일하지 않기 때문일 수 있습니다. 수평선 등.
3) 끝면에 Burr가 발생합니다.바 재료를 톱질할 때 일반적으로 최종 절단 부분에 버가 나타나는 경향이 있습니다.Burr가 있는 블랭크는 가열 시 국부적인 과열 및 과열이 발생할 가능성이 높으며 단조 시 쉽게 접히고 균열이 발생합니다.한 가지 이유는 톱날이 노화되었거나 톱니가 마모되어 충분히 날카롭지 않거나 톱날의 이빨이 부러졌기 때문입니다.두 번째는 톱날 라인 속도가 제대로 설정되지 않았다는 것입니다.일반적으로 새 톱날은 더 빠를 수 있고 오래된 톱날은 더 느립니다.
4) 단면에 균열이 있습니다.재료의 경도가 고르지 않고 재료 편석이 심한 경우 단면 균열이 발생하기 쉽습니다.단부 균열이 있는 블랭크의 경우, 단조 중에 균열이 더욱 확대됩니다.
블랭킹 품질을 보장하기 위해 생산 과정에서 다음과 같은 예방 관리 조치가 취해졌습니다. 블랭킹 전에 공정 규정 및 공정 카드에 따라 재료 브랜드, 사양, 수량 및 제련로(배치) 번호를 확인하십시오. .그리고 둥근 강철 막대의 표면 품질을 확인하십시오.블랭킹은 단조번호, 소재브랜드, 규격, 용해로(배치)번호에 따라 일괄적으로 실시하며, 순환추적카드에 블랭크 개수를 표시하여 이물질 혼입을 방지하며;자재 절단 시에는 '1차 검사', '자체 검사', '순찰 검사' 시스템을 엄격하게 실시해야 합니다.블랭크의 치수 공차, 끝 기울기 및 끝 버는 공정 요구 사항에 따라 자주 검사되어야 하며 검사가 적합하고 제품 상태가 표시됩니다.순서는 나중에 변경될 수 있습니다.블랭킹 과정에서 블랭크에 접힘, 흉터, 끝 균열 및 기타 눈에 띄는 결함이 있는 경우 적시에 폐기하도록 검사관 또는 기술자에게 보고해야 합니다.블랭킹 현장은 깨끗하게 유지되어야 하며, 다양한 재료 등급과 제련로(배치) 번호, 사양 및 치수를 별도로 배치하고 혼합을 방지하기 위해 명확하게 표시해야 합니다.재료 대체가 필요한 경우 재료 대체 승인 절차를 엄격히 준수해야 하며 재료는 승인 후에만 배출될 수 있습니다.
2 가열 과정.
반 샤프트 생산 공정은 두 번의 화재로 가열되고, 자유 단조 빌렛은 가스로로 가열되고, 금형 단조는 유도 전기로로 가열되므로 가열 순서의 예방 제어가 더 복잡하고 어렵습니다.가열 품질을 보장하기 위해 다음과 같은 품질 사양을 공식화했습니다.
가스 렌지가 가열되면 고온 영역에서 재료를 직접 충전하는 것이 허용되지 않으며 블랭크 표면에 불꽃을 직접 분사하는 것도 허용되지 않습니다.전기로에서 가열할 때 블랭크 표면이 기름으로 오염되어서는 안 됩니다.가열 사양은 해당 단조 공정 규정의 요구 사항에 따라 구현되어야 하며, 가열 매개변수가 안정적이고 신뢰할 수 있음을 입증하기 위해 교대 전에 블랭크 5~10개에 대한 가열 온도를 완전히 검증해야 합니다.장비 및 공구 문제로 인해 빌렛을 제 시간에 단조할 수 없습니다.냉각하거나 용광로에서 처리할 수 있습니다.푸시된 빌렛은 별도로 표시하고 보관해야 합니다.빌렛은 반복적으로 가열할 수 있지만 가열 횟수는 3회를 초과할 수 없습니다.블랭크가 가열될 때 재료 온도는 적외선 온도계를 사용하여 실시간 또는 정기적으로 모니터링하고 가열 기록을 작성해야 합니다.
3 빌렛 제작 과정.
빌렛 제작 중 일반적인 결함으로는 중간 빌렛 로드의 과도한 직경이나 길이, 표면 해머 자국, 불량한 계단 전환 등이 있습니다.로드의 직경이 너무 양수이면 금형 단조 중에 캐비티에 삽입하기가 어렵습니다.로드가 작은 경우 단조 중 로드의 큰 간격으로 인해 단조의 동축성이 너무 나빠질 수 있습니다.표면 해머 자국 및 불량한 단조 전환이 발생할 수 있습니다. 최종 단조품 표면에 패임이나 주름이 생길 수 있습니다.
4 다이 단조 및 트리밍 공정.
반샤프트 금형 단조 공정의 주요 결함으로는 접힘, 충전 부족, 압력 부족(타격하지 않음), 정렬 불량 등이 있습니다.
1) 접습니다.반축의 접힘은 플랜지의 끝면, 스텝 필렛 또는 플랜지의 중간에서 일반적이며 일반적으로 호 모양 또는 반원형입니다.접힘의 형성은 블랭크 또는 중간 블랭크의 품질, 금형의 설계, 제작 및 윤활, 금형과 해머의 체결, 단조의 실제 작업과 관련이 있습니다.접힘 현상은 일반적으로 단조품이 적열 상태일 때 육안으로 관찰할 수 있지만, 일반적으로 후기 단계에서 자분탐상 검사를 통과할 수 있습니다.
2) 부분적으로 불만이 가득합니다.세미 샤프트 단조품의 부분적인 불만족은 주로 로드 또는 플랜지의 외부 둥근 모서리에서 발생하며, 이는 둥근 모서리가 너무 크거나 크기가 요구 사항을 충족하지 못하기 때문에 나타납니다.불만족시 단조품의 가공공차가 감소하게 되며, 심각할 경우 가공을 폐기하게 됩니다.불만족스러운 이유는 다음과 같습니다. 중간 빌렛 또는 블랭크의 설계가 불합리하고 직경이나 길이가 적합하지 않습니다.단조 온도가 낮고 금속 유동성이 좋지 않습니다.단조 금형의 윤활이 불충분합니다.다이 캐비티 내 산화물 스케일 축적 등
3) 잘못된 배치.정렬 불량은 분할 표면을 따라 단조품의 아래쪽 절반에 대한 단조품의 위쪽 절반의 변위입니다.잘못된 배치는 가공 위치 지정에 영향을 미치므로 로컬 가공 여유가 부족해집니다.이유는 다음과 같습니다: 해머 헤드와 가이드 레일 사이의 간격이 너무 큽니다.단조 다이 잠금 간격의 설계가 불합리합니다.금형 설치가 좋지 않습니다.
5 트리밍 과정.
트리밍 공정의 주요 품질 결함은 잔존 플래시가 크거나 고르지 않은 것입니다.잔존 플래시가 크거나 고르지 않으면 가공 위치 지정 및 클램핑에 영향을 미칠 수 있습니다.국부적인 가공 공차의 증가와 더불어 가공 편차도 발생하며, 간헐적인 절삭으로 인해 절삭이 발생할 수도 있습니다.그 이유는 트리밍 다이의 펀치, 다이의 간격이 적절하게 설계되지 않았거나 다이가 마모되고 노화되었기 때문일 수 있습니다.
위에서 언급한 결함을 방지하고 단조품의 품질을 보장하기 위해 당사는 일련의 예방 및 통제 조치를 공식화하고 채택했습니다. 설계 검토 및 공정 검증을 통해 적절한 블랭크 또는 중간 블랭크 크기를 결정합니다.기존 금형을 제외한 금형 설계 및 검증 단계에서 캐비티 레이아웃, 브릿지 및 사일로 설계 외에도 접힘 및 잘못된 이동을 방지하기 위해 스텝 필렛 및 잠금 간격에 특별한 주의를 기울였으며 공정의 엄격한 품질 관리가 이루어졌습니다. 블랭킹, 가열 및 자유 단조 빌렛을 만들고 빌렛의 경사면에 초점을 맞춥니다.단면의 각도 및 버, 중간 빌렛의 계단 전이, 로드 길이 및 재료 온도.
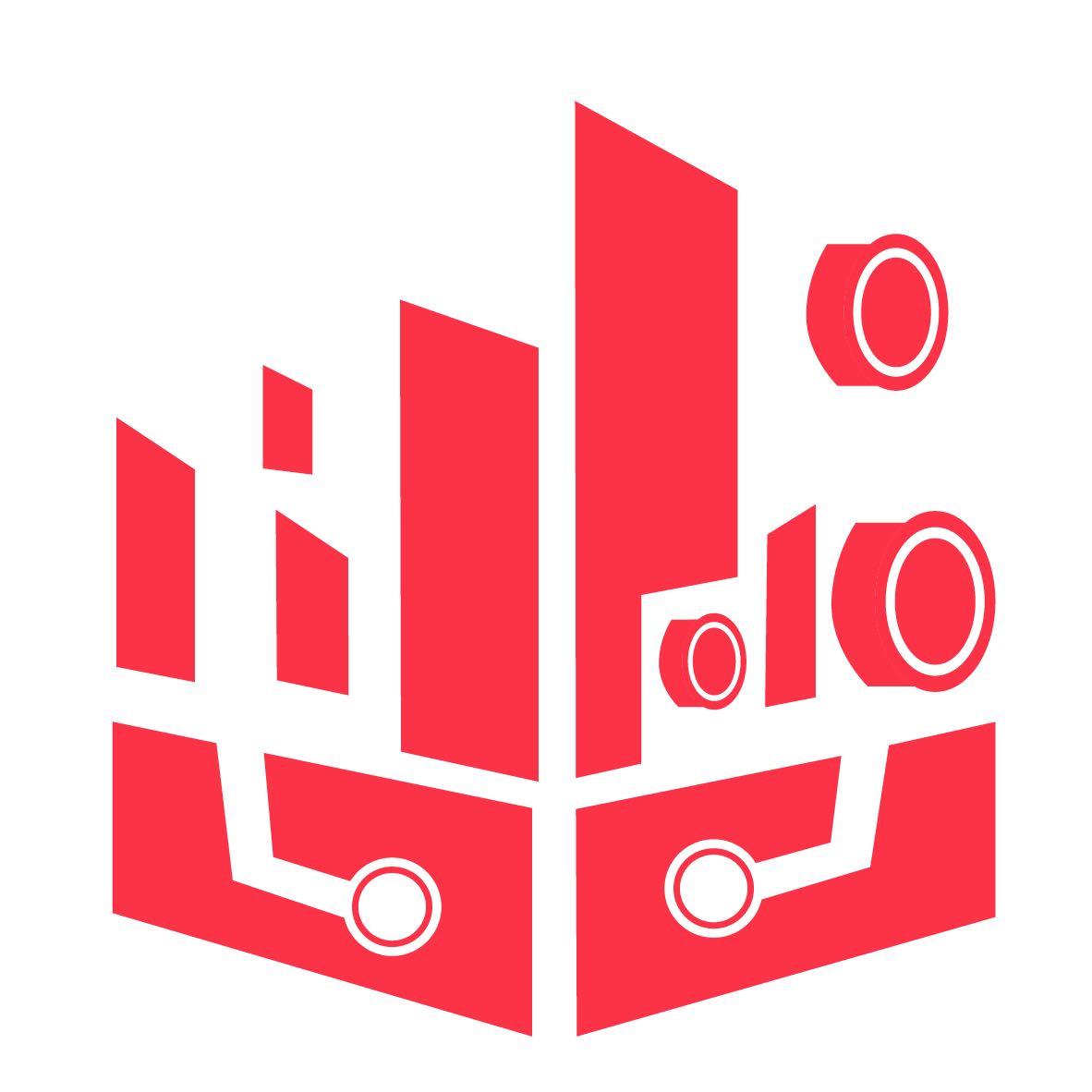
특징
부품 번호 P150700004
응용 PM 트럭 장착형 콘크리트 펌프
포장 유형

포장
1. 내마모성과 충격에 강합니다.
2. 품질이 안정적이고 신뢰할 수 있습니다.

우리 창고

